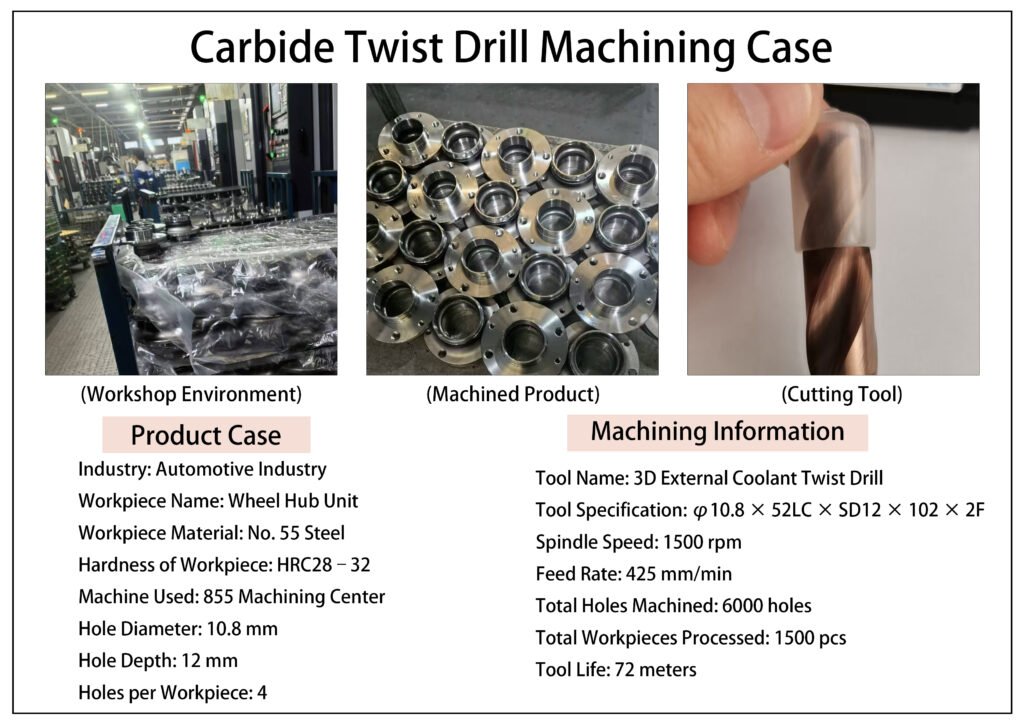
Industry: Automotive
Tool Application: Twist Drill Machining Case
Workpiece: Wheel Hub Unit
In the automotive manufacturing industry, precision and consistency are critical. In this case study, we showcase the successful application of a 3D external coolant twist drill for high-efficiency drilling of wheel hub units made from No. 55 steel with a hardness of HRC28–32.
Workshop Conditions & Setup
The machining was performed on a 855 vertical machining center, equipped for stable and efficient drilling under high feed rates. The target component—the wheel hub unit—requires four holes per part, each with a diameter of 10.8 mm and a depth of 12 mm.
Cutting Tool Used
- Tool Name: 3D External Coolant Twist Drill
- Specification: φ10.8 × 52LC × SD12 × 102 × 2F
- Cooling Type: External coolant delivery
- Flute Count: 2 flutes
- Material: Solid carbide
This specially designed drill ensures optimal chip evacuation and tool life, especially when working with medium carbon steels such as 55#.
Machining Parameters
- Spindle Speed: 1500 rpm
- Feed Rate: 425 mm/min
- Total Holes Drilled: 6000
- Total Workpieces Processed: 1500 pcs
- Tool Life: 72 meters
Performance & Results
Throughout the batch production of 1500 wheel hub units, the 3D external coolant twist drill maintained excellent dimensional accuracy, surface finish, and chip evacuation. The total tool life reached 72 meters, demonstrating superior durability and performance in mass production environments.
This case reflects not only the stability of our machining setup but also the high quality and reliability of our twist drill product line. It’s an ideal solution for automotive part manufacturers seeking productivity and precision.